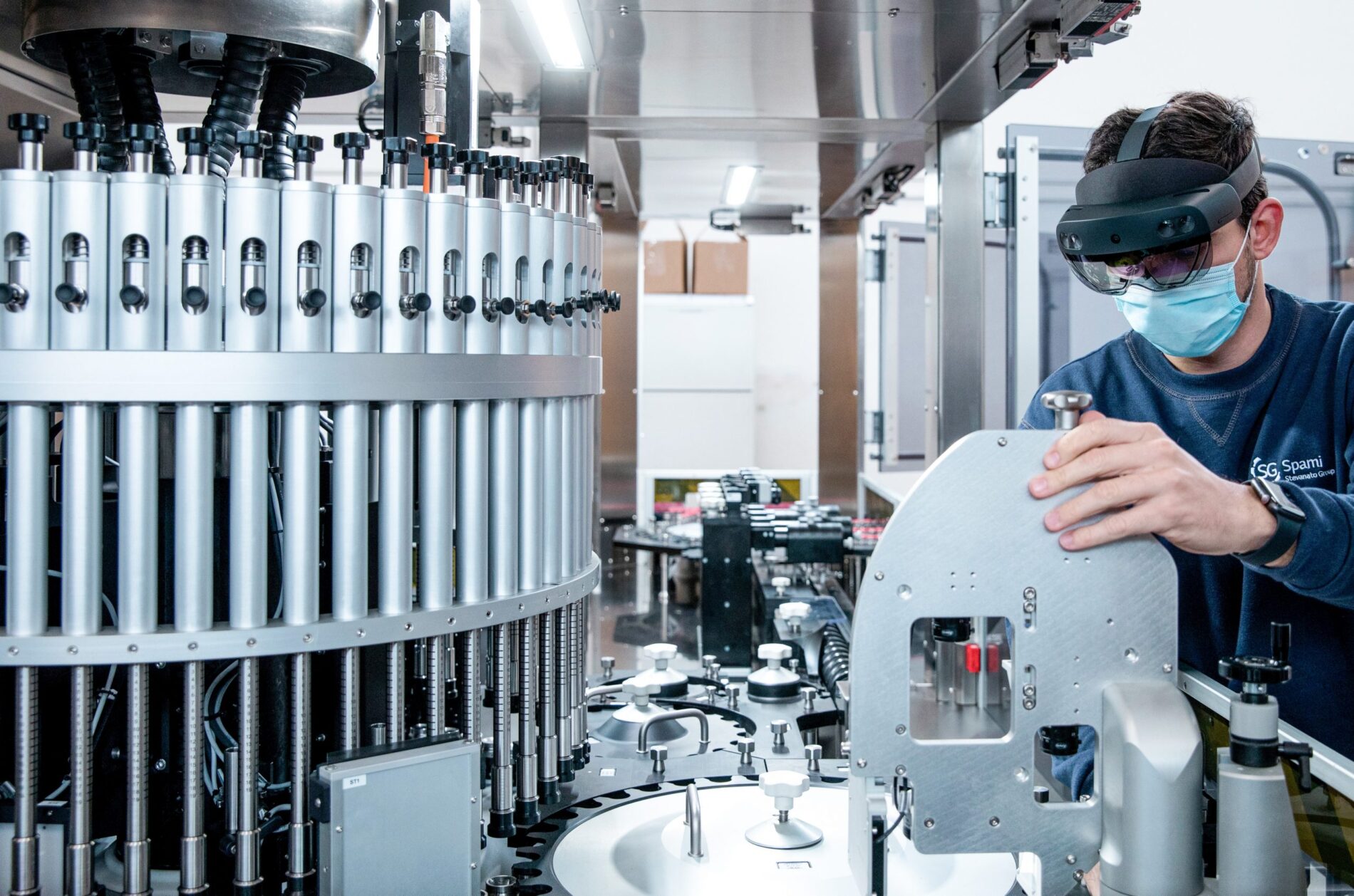
From lab to jab: How technology is supporting pharma equipment manufacturers to remain best in class
As the world continues to face numerous challenges from the impact of the COVID-19 pandemic, we have also seen how adversity can lead to innovation. In less than a year, we have gone from initial vaccine trials and testing, to administering concrete doses to vulnerable people around the world. So far, more than 560 million doses have been given – and counting. This makes it the biggest coordinated vaccination campaign in human history.
Alongside the scientific feats that brought us where we are, the vaccine rollout also involves a hugely complex logistical effort. One vital link in this chain is the rapid production of sufficient glass vials to contain the vaccines and enough syringes to deliver them. This needs to happen without compromising quality; a non-negotiable when it comes to something as valuable and vulnerable as a vaccine. Italian company Stevanato Group is turning to innovative technology to help deliver on both.
Positive pressure from the pandemic
The company, which has several locations worldwide including the U.S., Mexico and Japan, became involved in the pandemic response early. In addition to delivering glass vials and syringes to more than 70% of the global treatment and vaccine programs in the most advanced development stages (Phase 1 to 3), they produce plastic components used in virus detection kits and build essential vaccine inspection equipment used by several global pharmaceutical companies to ensure the integrity of their vaccines.
Given the company’s products play a role at almost every stage from testing to vaccination, ensuring business continuity while keeping on-site employees safe has been a business priority. Collaboration tools such as Microsoft 365 and Microsoft Teams have played a significant role in ensuring limited disruption and helping to connect colleagues, as well as customers, as much as possible.
“We all understand the very real impact that our work has on the world,” says Raffaele Pace, Engineering Vice President of Operations at Stevanato Group. “If, for instance, we deliver vaccine inspection equipment late to our customers, that has a knock-on effect on vaccine supply chains. That kind of positive pressure is a plus, as it makes you feel like you can make a difference.”
Necessity is the mother of innovation
The pandemic also caused the company to shift to conducting remote testing on the inspection equipment they sell to pharmaceutical companies around the world.
The factory acceptance test (FAT) is the final pre-delivery test that assures the customer their equipment is functioning properly and allows the company to troubleshoot any outstanding issues. It usually takes place in person at Stevanato Group’s facilities in Italy or Denmark before the final delivery, but as the pandemic swept through Italy and the rest of Europe in early 2020, it became clear this way of working was no longer viable, yet the need for quality inspection equipment was more pressing than ever. To solve this dilemma, Stevanato Group began offering customers the option of using mixed reality technology to attend factory acceptance tests remotely for all its equipment portfolio, including glass converting lines and assembly and packaging solutions.
Members of the company’s engineering teams wear a Microsoft HoloLens 2 headset and literally walk each customer through their equipment inspection process, demonstrating the different machine components, showing the customer how to run it, and sharing important documentation in real-time – all while the customer may be on the other side of the world.
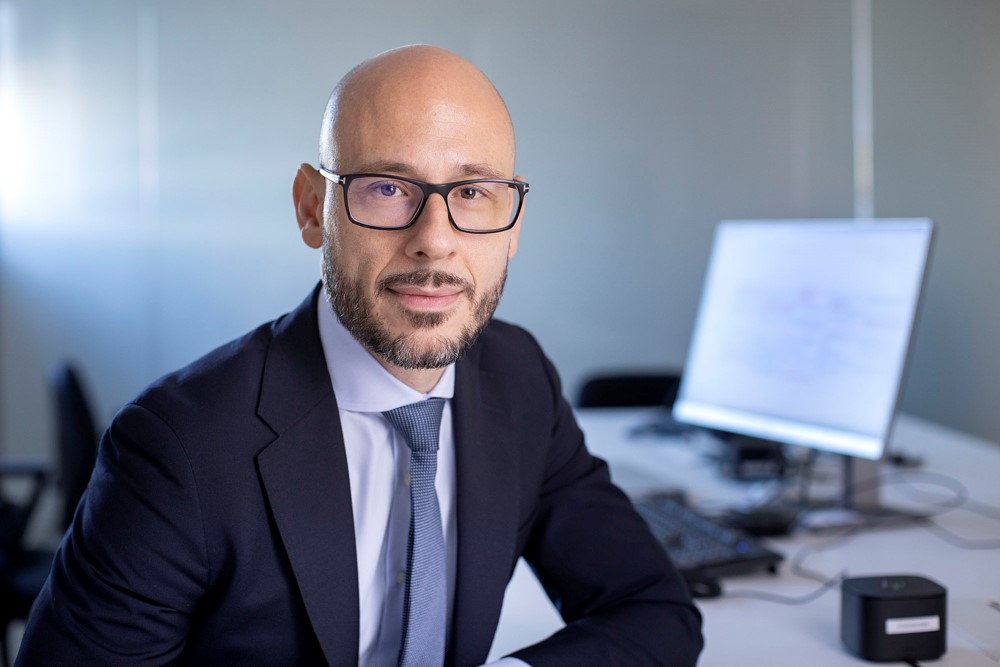
“Some customers were hesitant at first – but once they experienced the technology firsthand, they realized the advantages even beyond the pandemic, particularly from a cost and time perspective, when you eliminate the need to travel,” says Pace.
The impact of this innovation has been significant – not only are all FATs for Stevanato Group’s vision inspection machines now done 100% virtually, the technology has also shown its value earlier on in the inspection process. Since traditional, in-person FATs are one of the last stages before equipment delivery, misunderstandings or issues can arise that need to be resolved on a very tight deadline. Now, there’s no limit to how many times the customers can “see” the equipment for themselves.
The team has also started offering remote audits and mixed reality meetings to involve customers in a more hands-on way sooner in the production process. For instance, by using HoloLens 2 for early design review meetings, they can clarify the process, address any concerns and give the customer a real-time sense of how their equipment is evolving – all of which helps reduce the likelihood of delays and issues that might impact the wider production of medicines.
To improve production efficiency, Stevanato Group has also integrated AI into its inspection technologies. The company now has inspection machines featuring AI that pharmaceutical companies can use on site to inspect containers and ensure drug integrity. Though the machines already use cameras to detect irregularities in products at speeds and consistencies far exceeding human vision capability, the addition of AI and deep learning allows them to increase productivity and improve product quality, while complying with strict pharmaceutical data management and security requirements.
By leveraging these technologies, Stevanato and its customers can more easily detect defects in any product coming off the filling line, while also reducing the likelihood of the machine inaccurately detecting a defect (false positives). Such false positives can be reduced by tenfold, while the defect detection accuracy can be improved, yielding up to 99.9% accuracy. This also reduces the overall cost of ownership for such machines over time, making them more appealing to customers, as well as decreasing container production waste and related costs.

The greatest advantage of this system is that it increases the reliability of inspections, a key parameter for ensuring maximum container quality, conformity and medicine integrity and keeping patients safe, says Pace.
The company is also creating digital replicas of drug delivery device assembly equipment to improve the design, commissioning and operation phases of their projects. This digital twin technology offers data and insights on how to optimize processes in medical device assembly, enabling customers to reduce time to market and increase product quality.
Its advantages can be felt at all process phases: design and engineering, commissioning and production testing leading to risk mitigation and improved overall equipment efficiency (OEE). For example, in the design review phase it can help select the right concepts and elements before production, so process engineers can see the machine movements and identify potential issues.
“Led by people with a real sense of purpose, we are embracing digitalization,” says Pace. “We’re providing customers with faster, more advanced digital solutions that enhance equipment performance and ultimately help them get vital vaccines and medicines where they are needed, when needed.”