It’s that time of year again: The winners of the Microsoft Intelligent Manufacturing Award (MIMA) for 2025 have been chosen and get presented on the website www.MIMAwinners2025.com. The coveted prize, which Microsoft Germany awards together with the strategy consultancy Roland Berger, honors innovative manufacturing companies. This year, for the sixth time, MIMA is honoring groundbreaking solutions that are shaping the future of the industry, with a focus on operations. The winning teams were selected by a high-ranking jury of experts from industry, science and consulting firms.
“Accelerating future Operations!” – Under this motto, companies from the entire economic region of Europe, the Middle East and Africa (EMEA) have been called upon since November to submit their innovative digital solutions for the manufacturing, process, construction and automotive industries. Outstanding projects were sought in the categories Innovate!, Scale!, Add Value!, Disrupt!, Sustainability! as well as the overall winner of MIMA 2025. This time, the focus was on the area of operations, which encompasses all processes and activities required to manufacture products: from the planning, control and optimization of production processes, supply chain management, quality control and maintenance to personnel management.
From the best applications, 16 finalists were selected to present their projects at the Pitch Day on February 5. After extensive evaluations and discussions, the MIMA jury selected the six best projects that are particularly innovative and have the potential to lead the digital transformation across their industry. All MIMA 2025 winning solutions are based on artificial intelligence (AI), which is now an indispensable tool for the industry.
“Artificial intelligence is the crucial technology of our time. It enables completely new solutions for manufacturing that determine its future. And the Microsoft Intelligent Manufacturing Award honors the best ideas for this,” says Edith Wittmann, who is responsible for Microsoft Germany’s corporate customer business as Enterprise Commercial Lead. “This year’s winners impressively show how the use of AI leads to greater efficiency, better quality, new products and greater sustainability. The MIMA recognizes these achievements and thus promotes the progress of the entire industry.”
“Congratulations to all participants and winners for their remarkable achievements!”, says Jochen Gleisberg, Partner at Roland Berger and member of the expert jury. “We are pleased to award the MIMA 2025 to innovative pioneers in the field of operations. Our jury has selected the most effective and tangible smart industrial solutions in this field. In line with this year’s MIMA motto, they show how the pioneers of digitalization are accelerating the development of the operations of the future through AI.”
These are the winners of the Microsoft Intelligent Manufacturing Award 2025 in the various categories:
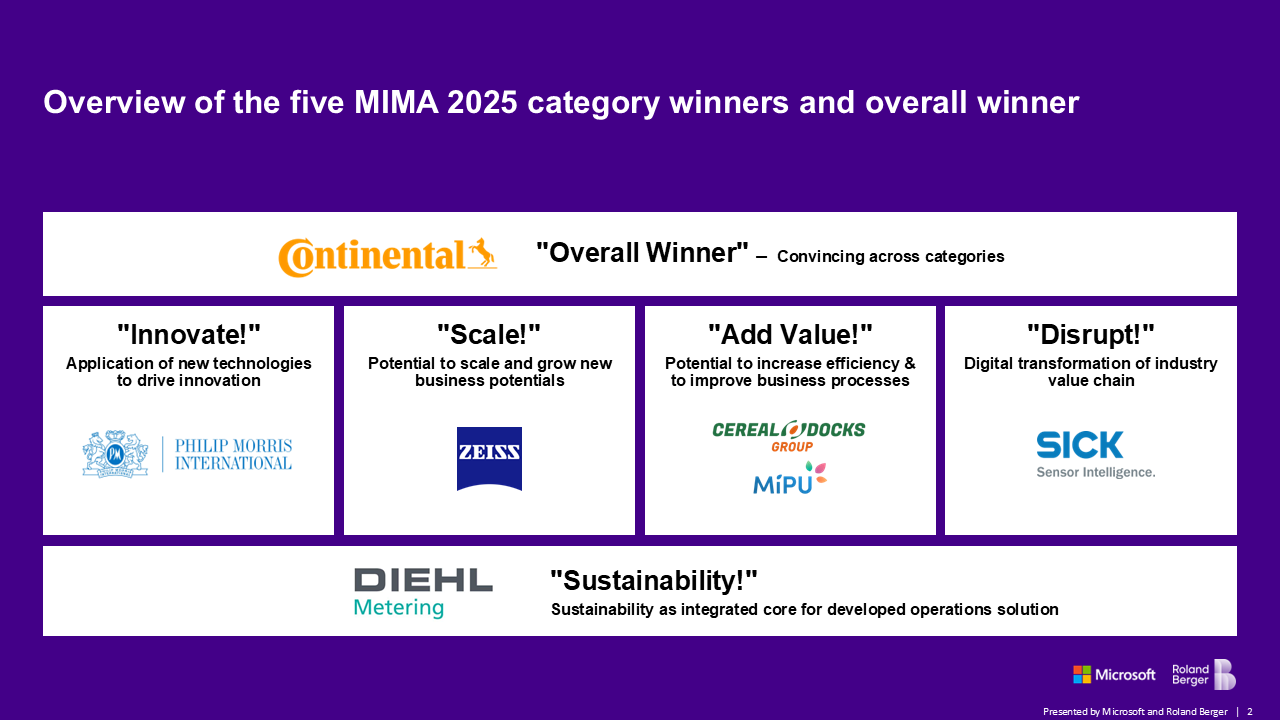
Philip Morris Manufacturing & Technology Bologna: Smart Factory combines innovation and sustainability (“Innovate!”)
Philip Morris Manufacturing & Technology Bologna has built a smart factory with a comprehensive digital architecture that uses AI and machine learning to optimize processes in real-time, as well as predictions that emerge from data analytics. As a result, the Italian company was able to secure the award in the “Innovate!” category. Its digital ecosystem spans from tobacco processing to production and distribution, ensuring traceability and efficiency. The use of digital twin technologies and the focus on sustainability have been able to reduce losses across the value chain. Philip Morris Manufacturing & Technology Bologna has shown that they can quickly test and deploy their innovations in a global network. This allowed them to demonstrate the scalability of their approach, which sees these digital solutions not only as experiments, but as an integral part of tomorrow’s production network.
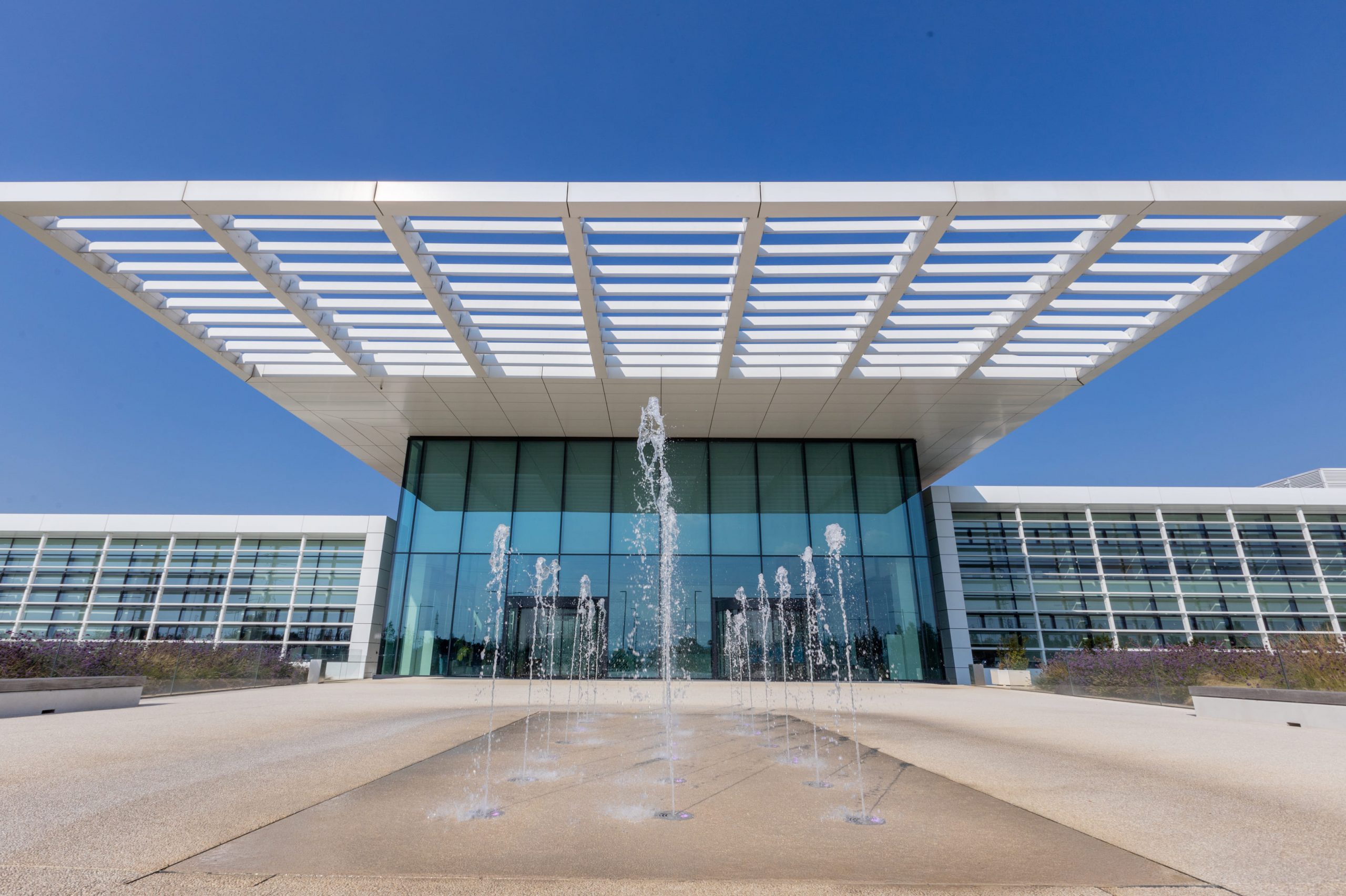
ZEISS Digital Innovation: Combined virtual and physical metrology for manufacturing (“Scale!”)
ZEISS Digital Innovation has developed an IIoT solution for machine-integrated process optimization in precision manufacturing that integrates quality assurance into the manufacturing process. The Dresden-based company has thus won the MIMA 2025 in the “Scale!” category. The combination of virtual and physical metrology can predict the quality of components in real time using digital solutions and enables immediate adjustments to production processes. Based on the closed-loop approach, the software solution has shown significant productivity gains and cost savings, achieving its return on investment (ROI) after just a few months. The numerous fields of application, especially in brownfield applications, and the positive effects demonstrated by ZEISS Digital Innovation’s customers underline its effectiveness and scalability in precision manufacturing.
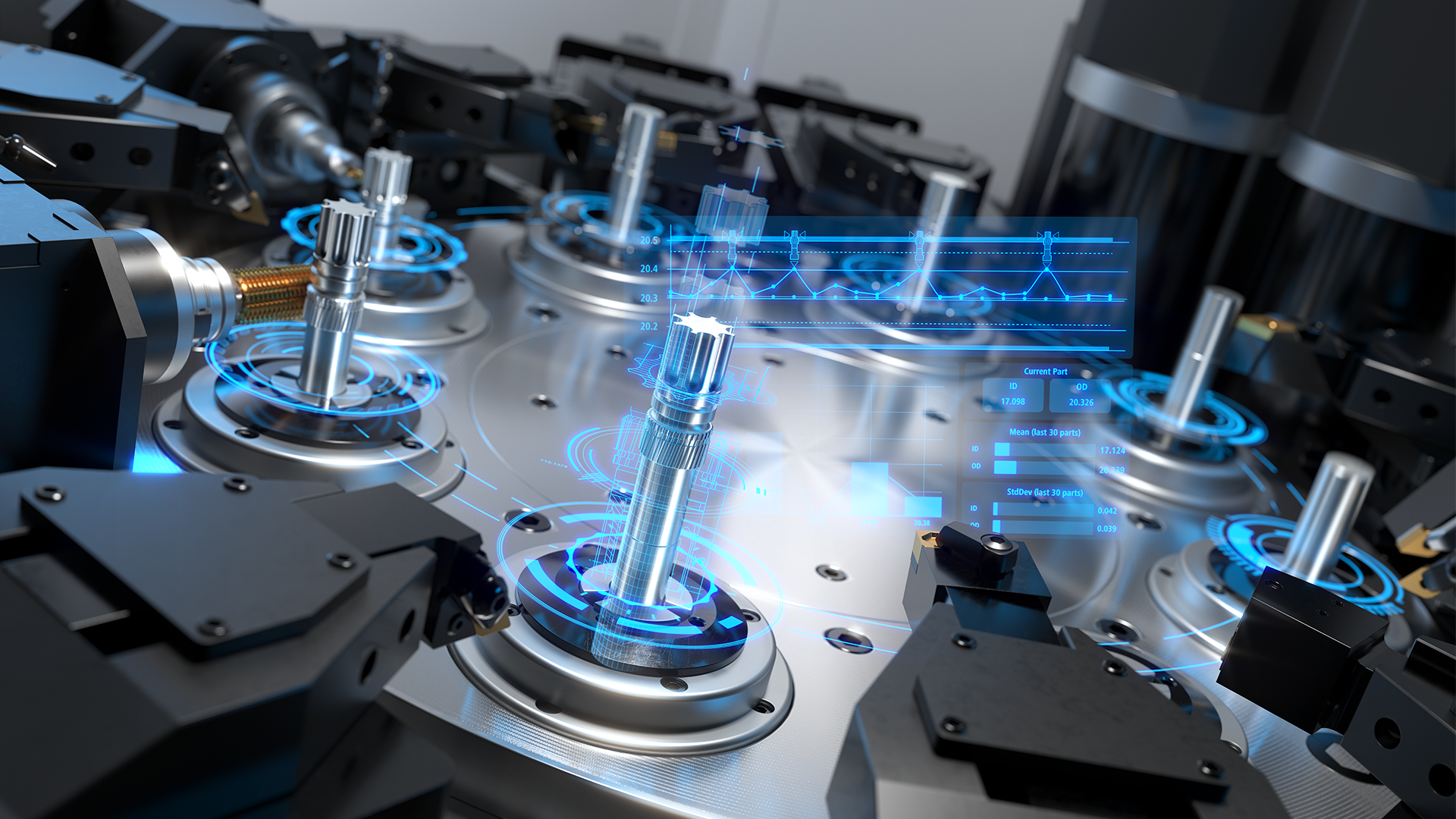
Cereal Docks and MIPU: Predictive factory for food production (“Add Value!”)
Cereal Docks, a multinational agrifood company, together with its technology partner MIPU, has introduced the Predictive Factory—a software and online service solution that leverages industrial data to precisely forecast machinery needs in terms of energy and maintenance. With this, they win the MIMA 2025 in the “Add Value!” category. By implementing this solution across eleven production sites, Cereal Docks has successfully optimized its manufacturing processes while increasing operational efficiency. The documented results include an 8 percent reduction in energy consumption without requiring hardware investments, a 20 percent decrease in maintenance man-hours, and a 98 percent reduction in unexpected machine failures.
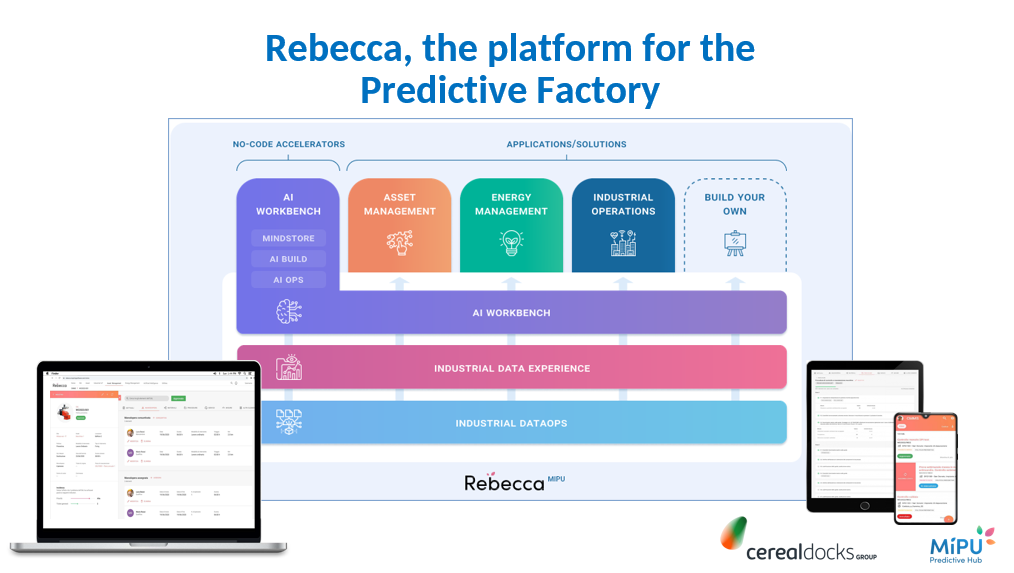
SICK: Predictive quality assurance through AI and real-time control (“Disrupt!”)
The sensor technology experts at SICK in Waldkirch have developed a groundbreaking AI-driven assistant system for manufacturing, earning them the MIMA 2025 in the “Disrupt!” category. This innovative dual approach combines predictive quality analytics with real-time process control to enhance production efficiency, reduce waste, and improve yield. The system analyzes production data to create a unique “fingerprint” of defective items, achieving an impressive 99 percent precision in predicting potential returns. At the same time, the integrated in-line process control system continuously tracks components in real time, proactively preventing defects before they occur. By providing real-time insights and feedback, this intelligent assistant system supports workers on the shop floor, streamlining processes and unlocking significant cost savings while offering scalable benefits across entire production lines.
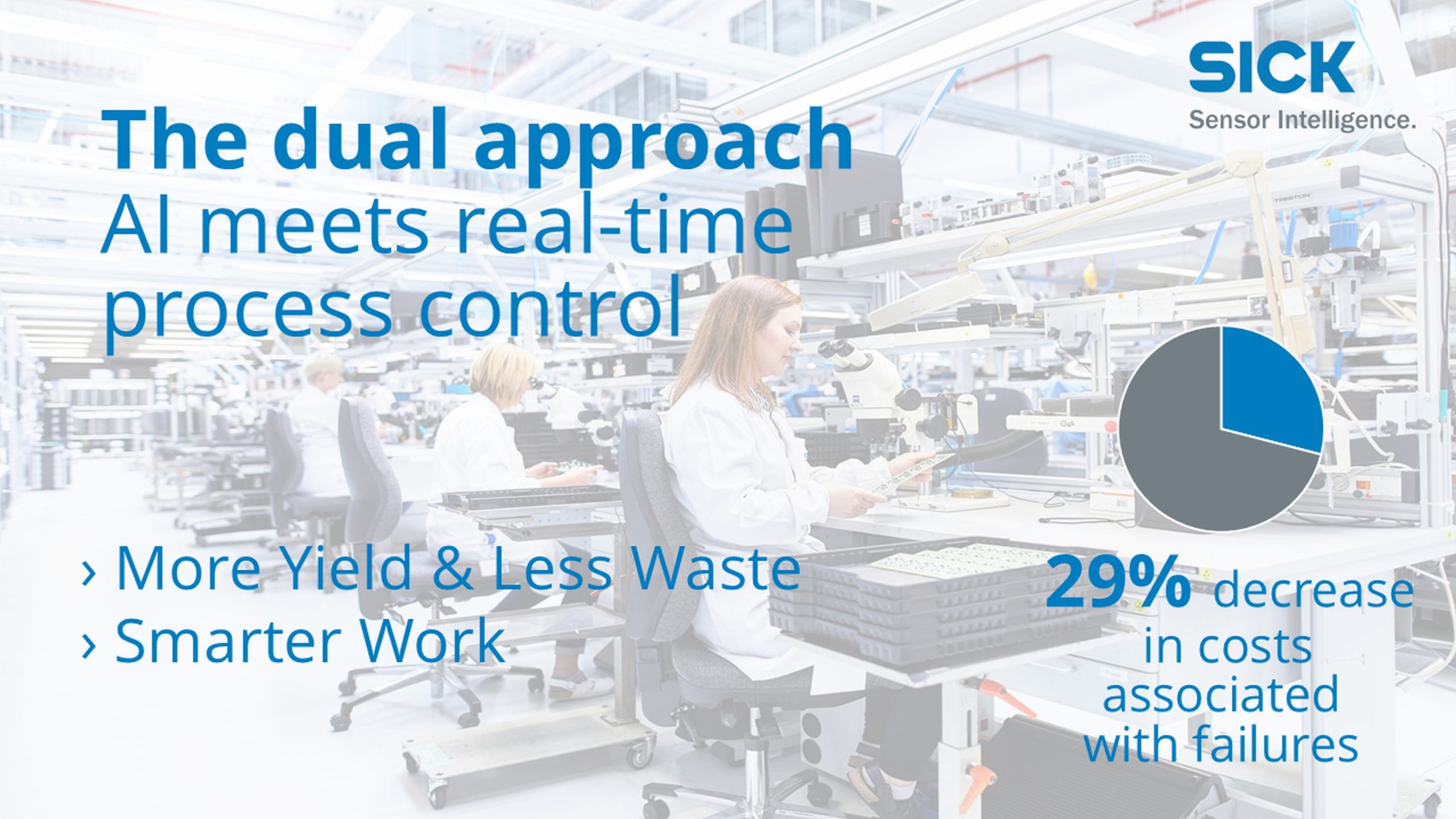
Diehl Metering: More sustainability through AI solution for less water losses (“Sustainability!”)
In the face of growing water scarcity in many countries, AI is now also revolutionizing industrial water management. And Diehl Metering in Nuremberg wins the MIMA 2025 in the “Sustainability!” category with such a solution. Depending on the region, up to 40 percent of pumped water is lost during distribution, which is exacerbated by an aging infrastructure and climate change. But through Diehl Metering’s „Sensor to Value Chain“ model, which is based on intelligent sensors and AI software, companies can improve the performance of their water networks. By leveraging large amounts of data, it makes it possible to detect leaks early, perform predictive maintenance, and monitor water quality. This reduces water losses, avoids costly production halts and makes it easier to manage large infrastructure investments. Diehl Metering’s AI-driven smart metering solution is designed for utilities and industries alike to ensure efficient and sustainable manufacturing as well as a safe water supply.
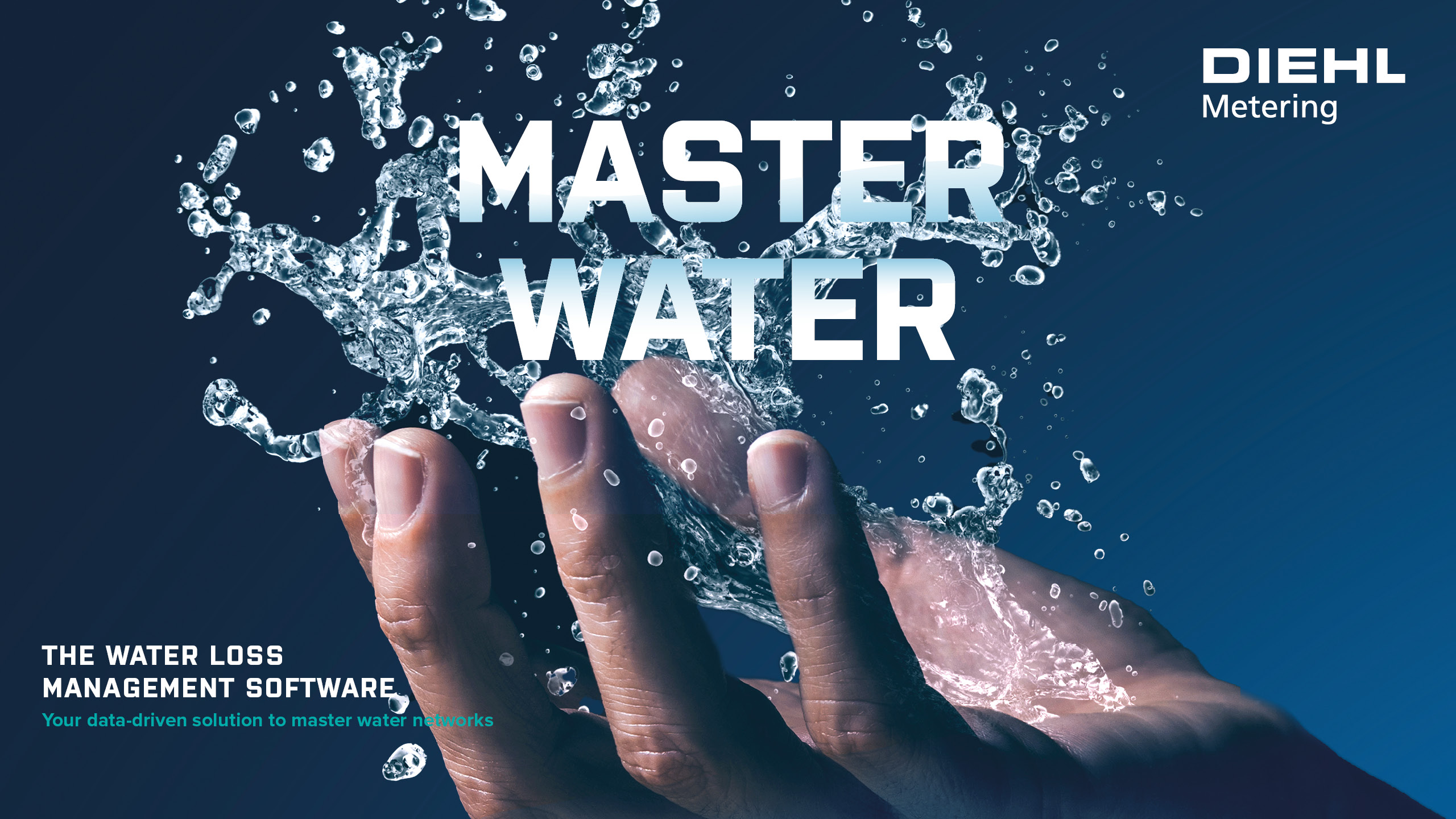
Continental: Overall Winner for AI-Driven Requirements Management
The overall winner of this year’s Microsoft Intelligent Manufacturing Award is Continental Automotive. The technology company has developed an AI solution for requirements management engineering: It extracts and classifies customer requirements from complex documents and maps them to existing product features. This significantly increases efficiency in handling up to 30,000 requirements per project. The new solution is about to be implemented at Continental Automotive swiftly, as it reduces the manual efforts for requirement extraction by up to 8 times and accelerates the market launch of new products. At the same time, it enables a more efficient use of resources in research and development. With this innovative tool, Continental is optimizing its entire requirements management process – not only for its customers but also for future suppliers.
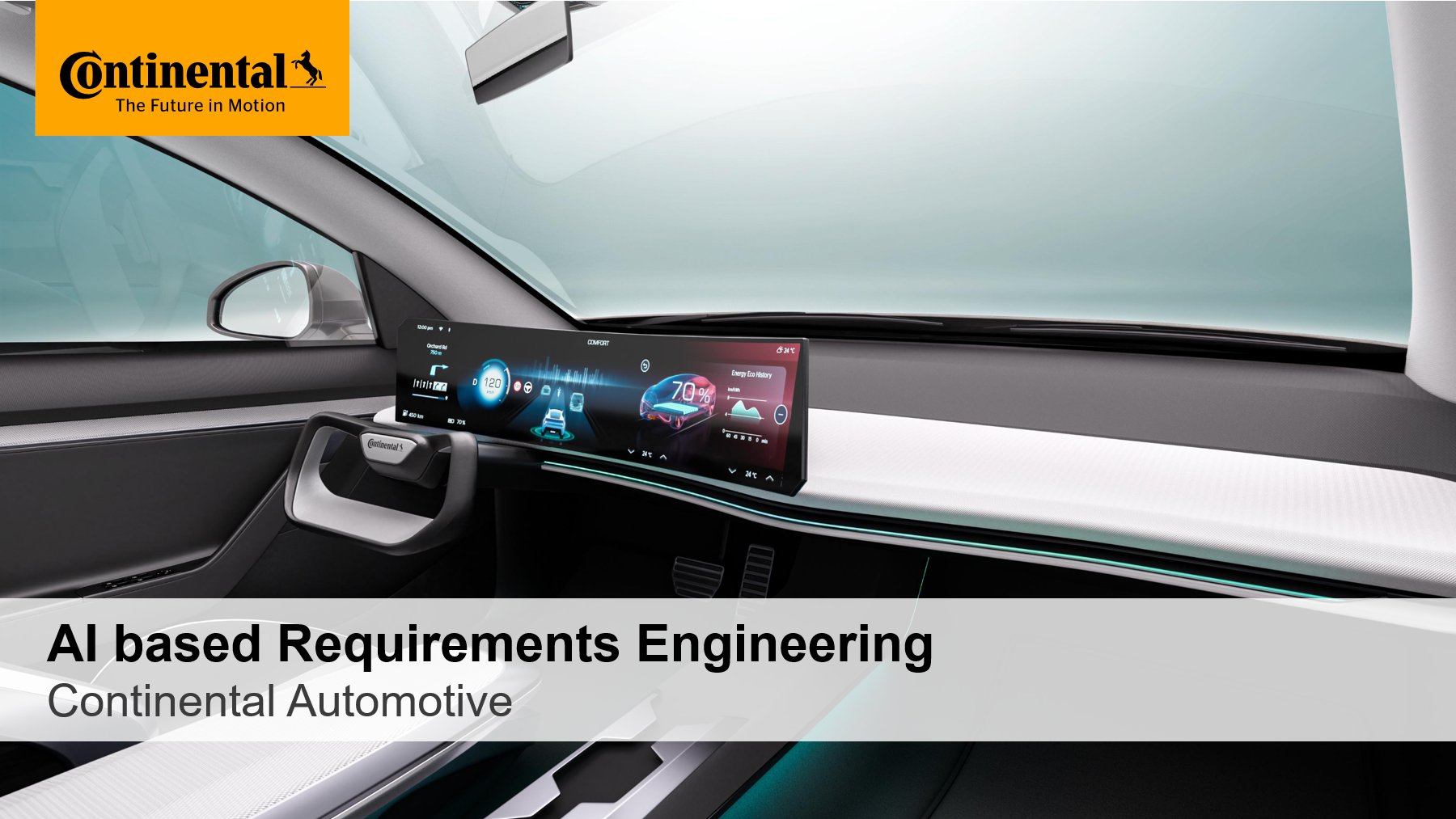
Admission to the MIMA Champions Circle
In addition to the six winners, 8 other finalists of this year’s competition will enter the exclusive MIMA Champions Circle:
- Aira (Sweden)
- Bosch Global Software Technologies (Germany)
- E.ON Grid Solutions (Germany)
- Kongsberg Digital (Norway)
- MTEK Industry (Sweden) (Common case with Aira, Sweden.)
- Sandvik (Sweden)
- Schneider Electric SE (France)
- Verifi (Saint-Gobain Construction Chemicals) (France)
Together with the winners of MIMA 2025, they will be part of an exclusive networking platform for technologically leading companies in the manufacturing industry, consisting of all finalists from previous years. A complete compilation of all award winners and finalists as well as a list of jury members can be found here: www.MIMAwinners2025.com.
More quotes from the winning companies:
Matteo Zompa, Director Manufacturing, Philip Morris Manufacturing & Technology Bologna:
“We are extremely proud to receive this recognition. The adoption of advanced digital technologies allows us to monitor and optimize production in real-time, ensuring traceability and greater efficiency. This award is a testament to the hard work and passion of our team and inspires us to continue pushing the boundaries of technology and innovation, with a strong commitment to practices that not only have a positive impact on our company but also on the environment in which we operate. Philip Morris’s mission towards a smoke-free future resonates with our own values, reinforcing our dedication to pioneering innovation.”
Alfred Mönch, COO, ZEISS Digital Innovation:
“Anyone who wants to ensure value creation in Germany and Europe in a future-proof and competitive manner, will have to implement autonomous solutions in the near future. This applies equally to complex production structures, such as in the semiconductor industry, and to traditional manufacturing disciplines such as machining. Wherever conventional efficiency measures reach their limits, we will see autonomous manufacturing solutions in the future. For us, the fundamental factor is the ability to use process and workpiece information in real time to control the manufacturing process. This is a major step towards data-driven production.”
Giulia Baccarin, CEO MIPU Predictive Hub, Cereal Docks and MIPU:
“The Predictive Factory is the only way to balance economic growth and sustainable production processes. AI allows us to turn industrial data into intelligence, helping manufacturers reduce waste, optimize resources, and create more resilient operations. This award recognizes the power of predictive technologies to shape a future where efficiency and sustainability go hand in hand.”
Dr. Niels Syassen, Executive Board Member for Technology & Solutions at SICK:
“We are honored to receive the MIMA 2025 for our disruptive use of industrial AI and sensor technology in manufacturing. By detecting and correcting defects in real-time, we empower our customers‘ workforce and unlock significant savings. At the same time, minimizing waste supports more sustainable production by lowering material consumption and reducing environmental impact. With this solution, we fully leverage manufacturing data to create real value for our customers.”
Annette Geuther, Chief Sales Officer at Diehl Metering:
“As industries strive for efficiency and sustainability, new technologies provide a game-changing approach, ensuring water is managed smarter and more resourceful. We see our AI-driven metering solution as more than an innovation — it’s a commitment to fight scarcity and securing water for future generations.”
Philipp von Hirschheydt, CEO Continental Automotive GmbH:
“At Continental, we continuously challenge the status quo to deliver smarter, faster, and more reliable solutions for our customers. By harnessing generative AI in Requirements Engineering, we are setting a new standard for efficiency and accuracy in automotive development. Winning the Microsoft Intelligent Manufacturing Award 2025 underscores our commitment to staying at the forefront of digital transformation—empowering our teams, partners, and customers with cutting-edge AI-empowered solutions.”
About Microsoft
Microsoft Deutschland GmbH was founded in 1983 as a subsidiary of Microsoft Corporation (Redmond, U.S.A.). In Germany, we employ over 3,000 people at our seven locations in Berlin, Frankfurt, Hamburg, Cologne, Munich, Stuttgart and Walldorf. Together with our 30,000 partners in Germany, we support companies with innovative solutions for the intelligent cloud and the intelligent edge so that they are successfully positioned for digital transformation. In addition, Microsoft is a global leader in many other areas such as productive software solutions, IT security, innovative hardware and development platforms that are also based on open source technology. We also connect more than 950 million people worldwide with our career network LinkedIn. With Xbox and Game Pass, we’re enabling a cross-platform gaming experience. In addition, Microsoft is involved in a wide range of initiatives and projects together with politics, business and science so that all people can participate in the progress of the digital society.
About Roland Berger
Roland Berger is one of the world’s leading strategy consultancies with a wide-ranging service portfolio for all relevant industries and business functions. Founded in 1967, Roland Berger is headquartered in Munich. Renowned for its expertise in transformation, innovation across all industries and performance improvement, the consultancy has set itself the goal of embedding sustainability in all its projects. Roland Berger revenues stood at more than 1 billion euros in 2023.
Contact Microsoft
Markus Göbel
Senior Commercial Communications Manager Innovation
E-Mail: [email protected]
LinkedIn
Contact Roland Berger
Raphael Dörr
Global Head of Corporate Communications & PR
E-Mail: [email protected]
www.rolandberger.com
Contact person PR agency Assembly Ltd.
Anica Thalmeier
Account Director
E-Mail: [email protected]