As today’s businesses continue their march to the drumbeat of Industry 4.0, new and innovative solutions continue to be developed around emerging technologies such as the Internet of Things (IoT), artificial intelligence (AI) and cloud computing, by companies that recognise the potential that these technologies offer, as well as the benefits that they can bring.
For Abrasive Engineering, a leading design and fabrication company, the combination of cloud and IoT technologies proved to be essential components in their digital transformation strategy. Their business focuses on the design and fabrication of blasting and shot peening machinery, as well as providing surface treatment services through blasting and shot peening.

A challenge in operational efficiency
Prior to embarking on their digital transformation journey, as there was no integrated system in place to both collect and analyse data on machine health, Abrasive Engineering relied heavily on engineers to make on-site visits to customer facilities for troubleshooting machinery, as well as to help their customers better optimise machine utilisation. What’s more, the lack of data on any emerging mechanical issues made it challenging to advise customers on the condition of their installed equipment.
Tan Ser Hean, Managing Director, Abrasive Engineering, noted that that the troubleshooting process required the manual collection of diagnostics data using physical flash drives; this added further time and complexity in managing the volume of customer support requests as the company expanded its client base across multiple industries.
“As we are progressing to expand our portfolio in the city-state, operational efficiency issues like the data collection process became a huge problem for us. Technology was the only way for us to solve this problem,” added Tan.
All in all, Abrasive Engineering was spending huge amounts of manpower and resources in managing manpower productivity, maintaining operational efficiency, as well as being able to maintain customer satisfaction levels. This was preventing the company from being able to properly scale and grow their business.
Leveraging IoT to optimise operations
To embark on their digital transformation journey, Abrasive Engineering partnered with the Agency for Science, Technology and Research’s (A*STAR) Advanced Remanufacturing and Technology Centre (ARTC).
“The solution to address Abrasive Engineering’s challenges was to harness the power of the cloud to obtain real-time insights on their customers’ machine performance. We helped AE adopt the Microsoft Azure IoT Box technology,” said Stuart Wong, Senior Group Manager, Smart Manufacturing Group, ARTC.
“The IoT Box, which is integrated with the Microsoft Azure IoT platform, enables Abrasive Engineering to collect data on their machine performance in real-time. To provide both Abrasive Engineering and their customers with greater visibility and insights into the collected data, we developed a dashboard to help present these insights and analytics in a clear, and easy-to-understand manner,” added Wong.
Via an internet connection, Abrasive Engineering’s customers can monitor their blasting and shot peening machines remotely at their convenience, while also being able to act if needed.
This IoT-enabled monitoring system has enabled Abrasive Engineering savings of up to 30 percent of man-hours spent on managing machine downtime per month, allowing them to allocate more time and employee resources into more value-added tasks such as developing newer and innovative solutions for their customers.
“By leveraging on Microsoft’s Azure Intelligent cloud platform, Abrasive Engineering has not only been able to deliver significant improvement in operational efficiencies, but also in empowering their employees to deliver a better customer experience,” said Gerald Leo, Commercial Partners and Small Medium Enterprises Group, Microsoft Singapore.
Empowering employees to fully embrace digital transformation
While it is obvious that adopting new technologies worked in Abrasive Engineering’s favour, the beginning of their digital transformation journey wasn’t exactly a smooth one, as there was a skills gap due to some employees not having a background in, or clear understanding of technology.
“When we first implemented Azure IoT Box, we had challenges getting everyone up to speed as not everyone on the team had the benefit of experience in IT. Nevertheless, through a comprehensive training and upskilling programme, our employees are now able to better understand how to capitalise on modern technologies such as IoT to serve our customers better,” shared Tan.
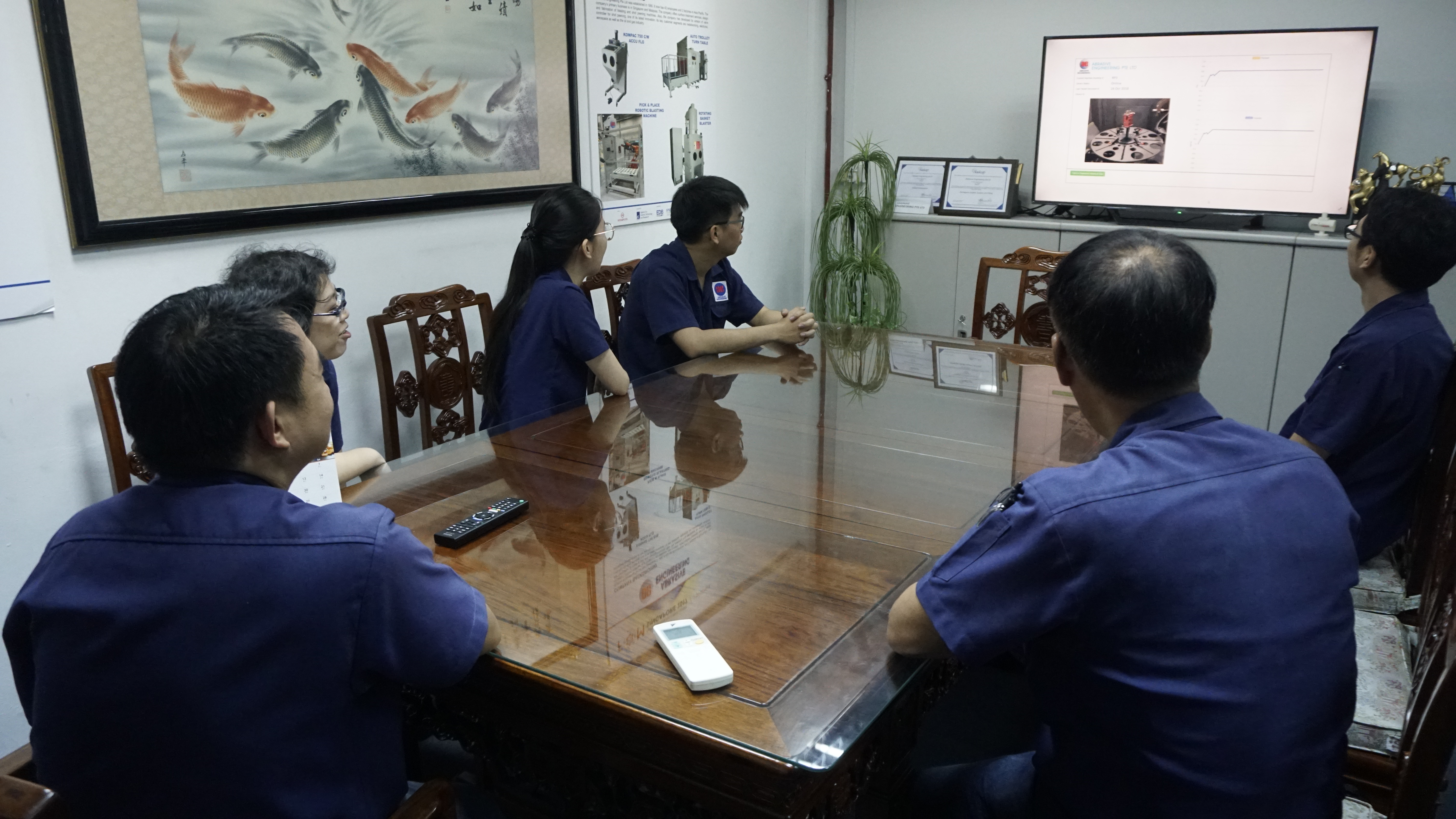
Embracing Industry 4.0 with smarter offerings
With the right technology and training in place, Abrasive Engineering is now positioned well to excel and reap the benefits of Industry 4.0. In the short term, Abrasive Engineering is looking to add even more value-added features to their monitoring system, and to explore other digital solutions to improve their machines’ performance further. At the same time, the company is also starting to think about creating innovative, differentiated product offerings to better satisfy their customer’s needs.
“Industry 4.0 is one of opportunity, and we’ve seen how new technologies have enabled us to move forward in optimising operations and serving our customers better. We’re looking forward to the possibilities that the future brings,” said Tan.