The total package: Tetra Pak’s technology keeps food and drink flowing safely from farm to table
The cows can’t wait.
This irrefutable fact of nature cascades from dairy farms – where each cow typically produces six gallons of milk every day – to food-processing companies funneling that white gold into cartons.
But when one part fails on a milk-packaging line, it can take the entire operation offline for days, leaving a plant unable to store thousands of soon-to-spoil gallons. And there’s no stopping the cows on the farm or the milk that must be harvested.
It’s an urgent reality in the dairy world – and in many factories that process and package perishables bound for grocery aisles.
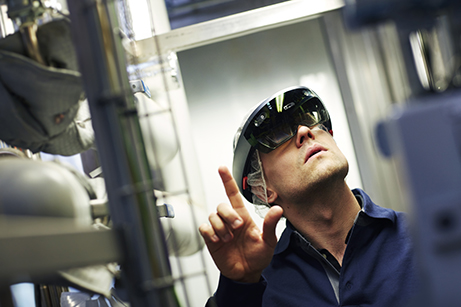
To prevent such disruptions across the food industry, packaging pioneer Tetra Pak is employing new, digital tools that enable its cloud-connected machines to predict exactly when equipment needs maintenance, averting many breakdowns. And when repairs are needed, Tetra Pak service engineers use HoloLens headsets to more quickly diagnose and fix machine issues, even in the most remote locations.
The Swedish company, which last year sold 188 billion packages and produced $12.2 billion in net sales, is transforming the services it offers to food and beverage manufacturers in more than 175 countries.
“We will take over a lot of risk on behalf of our customers. To do that, we need cutting-edge technologies to control and minimize these risks,” says Johan Nilsson, vice president of Tetra Pak Services. “When you have plants around the world, the service knowledge we gain from one plant comes to benefit another. This prevents issues from happening.”
In short, Tetra Pak can now foresee machine problems – or quickly spot breakdowns – reducing plant downtimes and the high costs they carry, Nilsson says.
The science of shelf life
This work is particularly vital to companies that process and package aseptic, or sterile, products. In the aseptic process, short heating and cooling times (275 degrees Fahrenheit for up to 15 seconds) ensure food is absent of harmful microorganisms while retaining its taste and nutritional benefits. The food is then packed in pre-sterilized cartons. An unopened aseptic package can be stored without refrigeration or preservatives for up to six months.
It’s a long-proven process, described by the Institute of Food Technologists as “the most significant food science innovation of the last 50 years.” Tetra Pak holds a central place in that history. At a 1961 press conference in Switzerland, the company presented the first machine for aseptically filled bacteria-free milk.
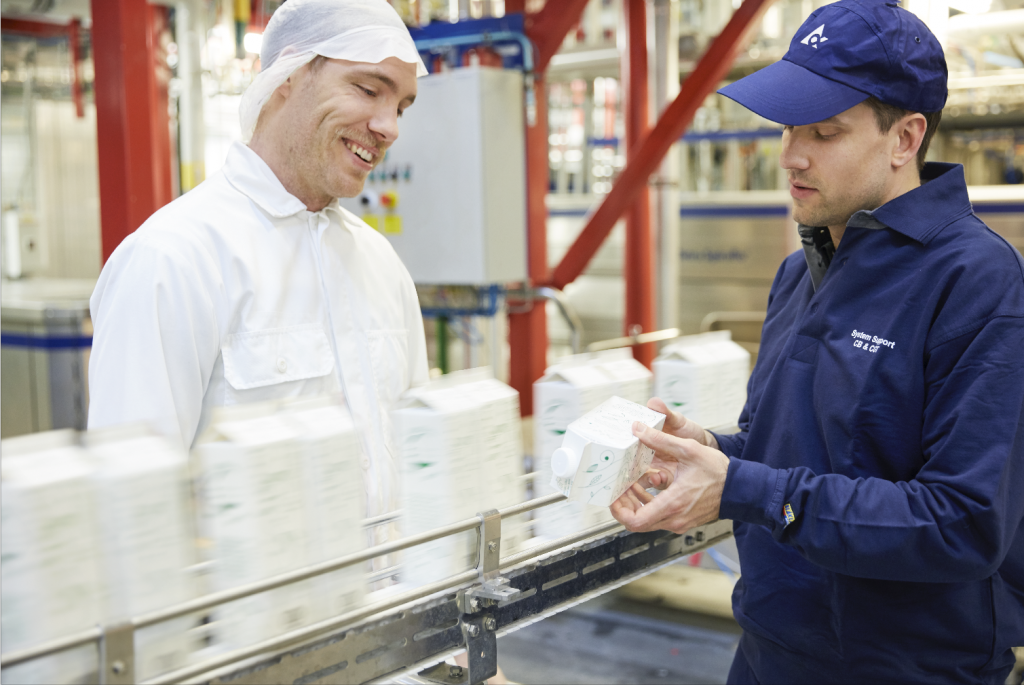
But more than 50 years later, it remains a delicate task to predict when to maintain aseptic equipment that may run around the clock. Do it too soon, a plant may unnecessarily swap out expensive parts well before they’re worn, adding costs. Do it too late, a plant may have to wait days to repair a machine and restart operations.
One of those integral machines, Nilsson says, is a servomotor – used in forming and sealing food packages. The motor’s usual lifespan varies between 2,000 hours and 7,000 hours. (Temperature and humidity affect that range.) A typical factory operates for about 4,000 hours a year, he adds.
“So it can be up to a year’s difference in when to change it,” Nilsson says. “You don’t want to over-maintain it. But if it breaks down, you have a catastrophic failure because a lot more parts get destroyed.
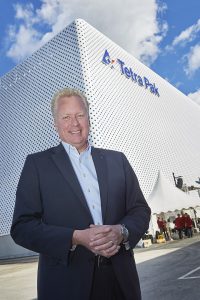
“You could then have a very long down time because the spare parts may not exist in a country where the customer is. It could take days to get parts there. It can be the difference between a four-hour, planned stop – where they might stop anyway to clean – and a four-to-five day loss of production where they can’t use any equipment at all,” he says.
By connecting packaging lines to the Microsoft Azure Cloud, Tetra Pak can collect operational data to help predict informed maintenance timing.
Case in point: The company has placed sensors on some carton-filling equipment, allowing global experts to analyze, in real time, data patterns in those factories against data from more than 5,000 other packaging lines.
During a recent, six-month period involving 11 packaging lines, the company predicted future breakdowns in five of those lines, spurring preventive maintenance and saving those customers more than $30,000, Tetra Pak leaders say.
An operational snapshot
Data that’s gleaned from connected machines gives company technicians an operational snapshot across more than 5,000 Tetra Pak packaging machines in use. That information helps service engineers swiftly answer critical questions, such as: When did a specific failure happen and how long did it last? What was that machine’s temperature at the time? What was the pressure?
The performance data is aggregated and available on technicians’ mobile devices.
“So if you’re a service engineer and you arrive at the customer, you can use a simple app to pull up the significant performance information from that customer,” Nilsson says. “You can drill down to see the performance, equipment by equipment.
“You are much more educated when you walk into the customer, and it becomes a much more informed and fact-based discussion between the service engineer and the customer,” Nilsson says.
To further streamline machine diagnostics and repair for customers, Tetra Pak is outfitting service engineers with hundreds of HoloLens devices, Microsoft’s mixed reality technology.
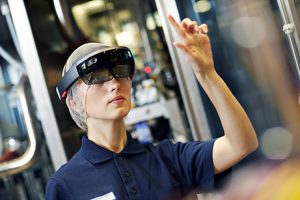
With those headsets, service engineers can make a Skype call to a Tetra Pak service center and speak to an expert with deeper knowledge of a specific machine. The expert remotely guides the engineer through a repair, cutting the time needed to fix the problem.
That tool can also reduce repair costs by making it unnecessary to dispatch a second service engineer to a plant to assist in the repair – a journey that could involve flying in another person from another country, Nilsson says.
“Customers have many pieces of equipment, so you have to know a lot of about a lot. That’s often difficult. This helps us to do that,” he says. “This is how we take the global expertise that we have available somewhere in Tetra Pak and bring it to the fingertips of the engineer in the countryside in Chile or Pakistan.”
Photos courtesy of Tetra Pak.