
The cloud and tires: Where the rubber and the Internet of Things hit the road
Making transportation more efficient and safer with data
How well a vehicle’s tires perform can save fuel, emissions, money, and, most importantly, lives.
While many private car drivers might give it little thought, the operators of bus, coach, and truck fleets know too well that having the right tire pressure is essential for an efficient, comfortable and safe journey.
Research in the United States – which has one of the world’s largest road transport sectors – ranks tire wear as a top line operating cost for commercial fleets. Blowouts also cause more than half of costly roadside breakdowns and can contribute to accidents.
Incorrect pressure not only means that tires wear out quicker, it is also a drag on vehicle performance and so raises fuel use. That’s bad both for the financial bottom line and the environment.
Maintaining optimum tire pressure sounds simple enough. But fleet managers know from experience that it’s hard to enforce. Everchanging temperatures, variable road conditions, different driving habits, cargo loads, tight schedules, and human error all play a part.
What’s true on the freeways of America is also true across the world. In Japan, the bright yellow coaches of the Hato Bus Company have been navigating the streets of Tokyo and beyond for decades, taking hundreds of tourists on daily sightseeing and transfer trips. With an ethos dedicated to safety, security, and reliability, the company has long practiced strict maintenance regimes.
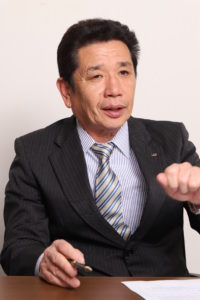
“Drivers check tires before starting daily services, and technicians check tires during monthly vehicle inspections,” says Yoichi Matsui, Executive Director of Hato Bus’s Sightseeing Bus Business Division, Vehicle Service Department. “There are seven tires on a large bus: two front wheels, four rear wheels, and one spare. We used to spend about 15 minutes per bus checking these tires manually, and inspections were prone to human error.”
Given the potential costs and risks involved, Hato Bus wanted a better monitoring system.
Enter Bridgestone – one of the largest tire manufacturers and innovators of tire technologies in Japan and the world. It has developed Tirematics – an Internet of Things (IoT) solution built on Microsoft Azure.
“Tirematics is a solution for commercial fleet operators,” explains Naoya Hamahata, Bridgestone’s Manager for Digital Solution Development. “Innovative sensors are attached to each tire and capture pressure and temperature (data) in real time and transmit information to our cloud platform. When an abnormality is detected, Tirematics immediately issues an alert to the appropriate person, such as the driver, tire technician, or maintenance manager.”
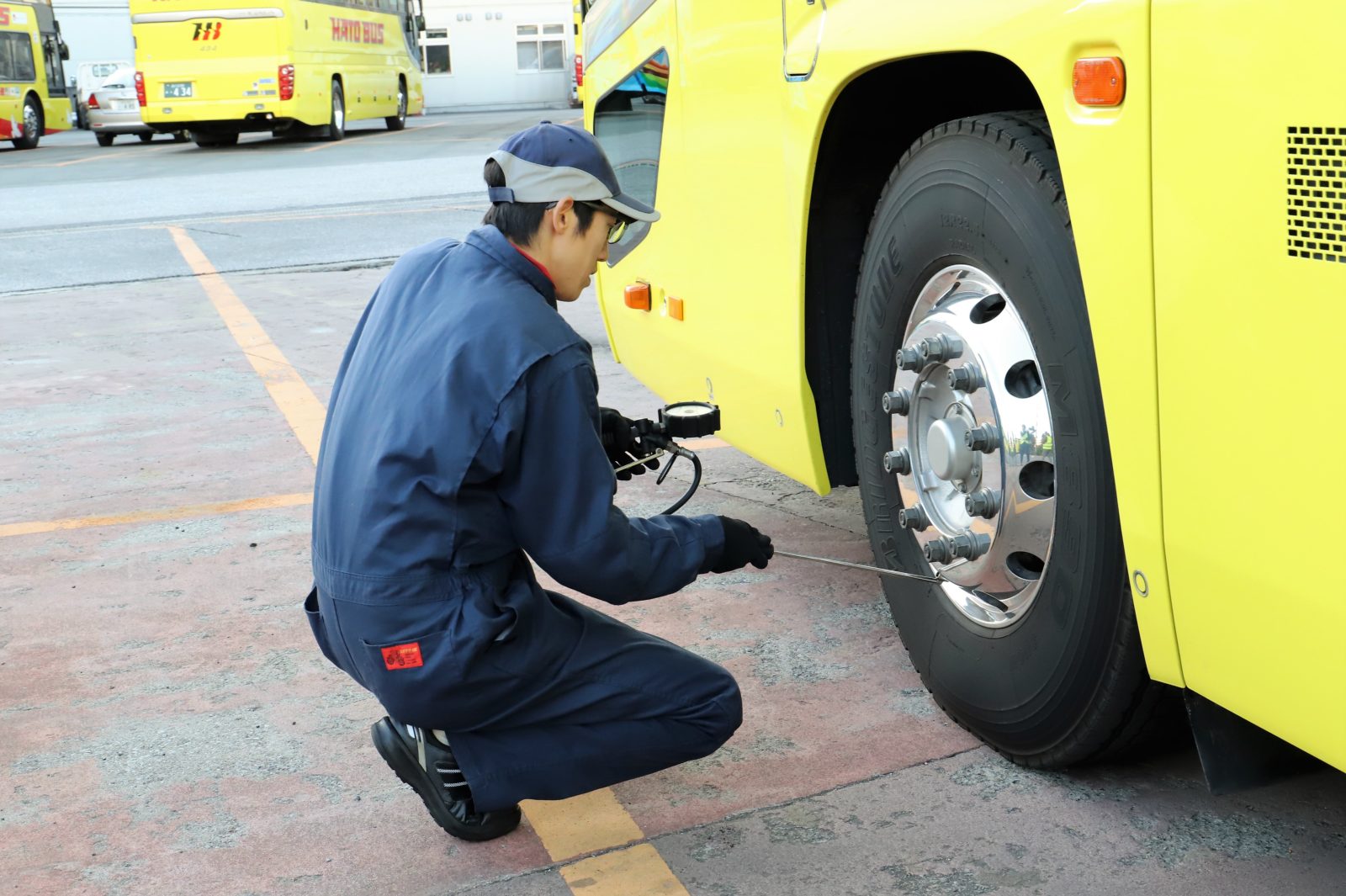
The result is reduced tire inspection and maintenance workloads along with fewer tire-related operating issues – including breakdowns and safety. Bridgestone started developing Tirematics on Azure in August 2016. The Tirematics architecture comprises Azure IoT Hub, Azure Data Lake, Azure Stream Analytics, Azure Event Hubs, and more.
It works like this: Tire sensors first send data to a local system at a vehicle maintenance site. The system then uses mobile phone networks to send the data to Azure IoT Hub and stores it on Azure Data Lake. Next, Azure Stream Analytics analyzes the data in real time. If the system detects an abnormality, Azure Event Hubs sends an alert.
Bridgestone completed Tirematics’ migration to Azure in May 2017 and started Japanese field tests last August in partnership with Hato Bus – which now responds to tire issues much faster thanks to the alerts that Tirematics sends via smartphone to its service managers.
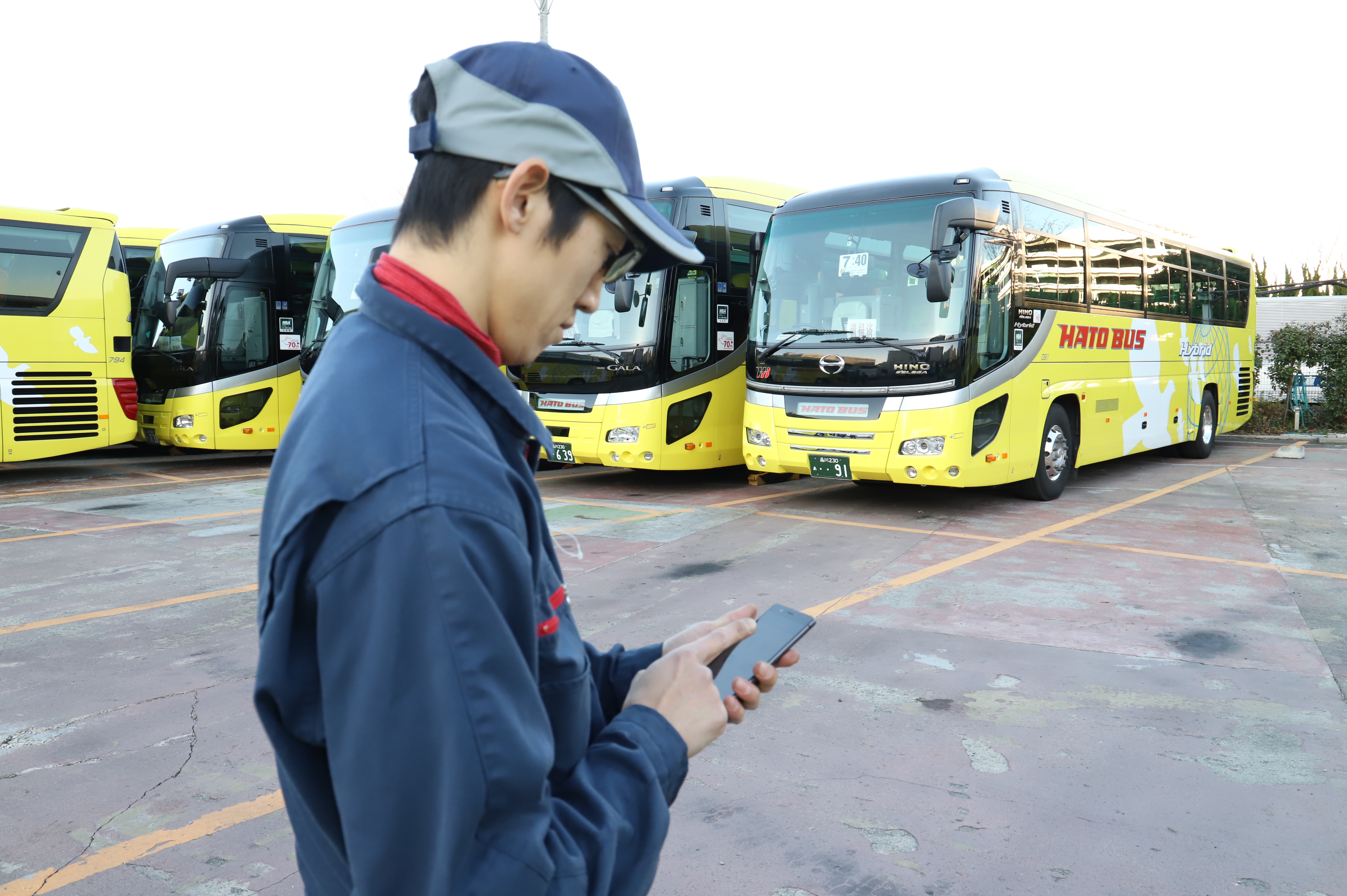
“We place the greatest emphasis on tires for the safe operation of our buses,” says Matsui from Hato Bus. “To reduce errors in readings and to give us complete visibility of our tire pressure conditions, we decided to implement a monitoring solution. Looking at the advances of technology and anticipating future mobility trends, we adopted Tirematics.
“Tirematics sends data and alerts directly to our managers. This allows us to respond to problems quickly without having to wait for our drivers to report.”
Bridgestone is now operating Tirematics in around 20 countries, delivering what Hamahata describes as “safer, smarter, and more economical mobility for the world.” He says the quality of Microsoft’s global support and Azure’s ability to scale are major differentiators in the cloud space. Bridgestone appreciates how well Azure coped with the expanded scale of Tirematics’ global deployment, he says.
Meanwhile, more innovation is coming. The automotive industry is becoming progressively Connected, Autonomous, Shared, and Electric (CASE) as it pushes for disruptive changes in personal and commercial mobility. With the advances in IoT and other technologies, it’s now possible to collect information from in-use tires and develop new services.
“Our innovation process is driven by answering our customers’ pain points and needs,” Hamahata says. “It requires us to provide a truly value-added service.”
Tirematics currently measures and collects tire pressure and temperature data, but its scope is likely to expand. Bridgestone has started tests to make features such as artificial intelligence available on third-party sensors via Azure IoT Edge. Bridgestone plans to provide the solution to more transportation operators and connect it to various systems, such as Toolbox, to create a tire data collection platform.
The company is also developing a system in which Bridgestone-trained data scientists will quickly and effectively analyze the data that Tirematics and other digital tools collect and store.
“Combining this system with our unique technologies will enable us to develop new technologies and tires,” says Hamahata. “We will continue to provide tires tailored to the needs of our customers and improve customer value by using data as the basis to enhance the quality of our proposals and services.”