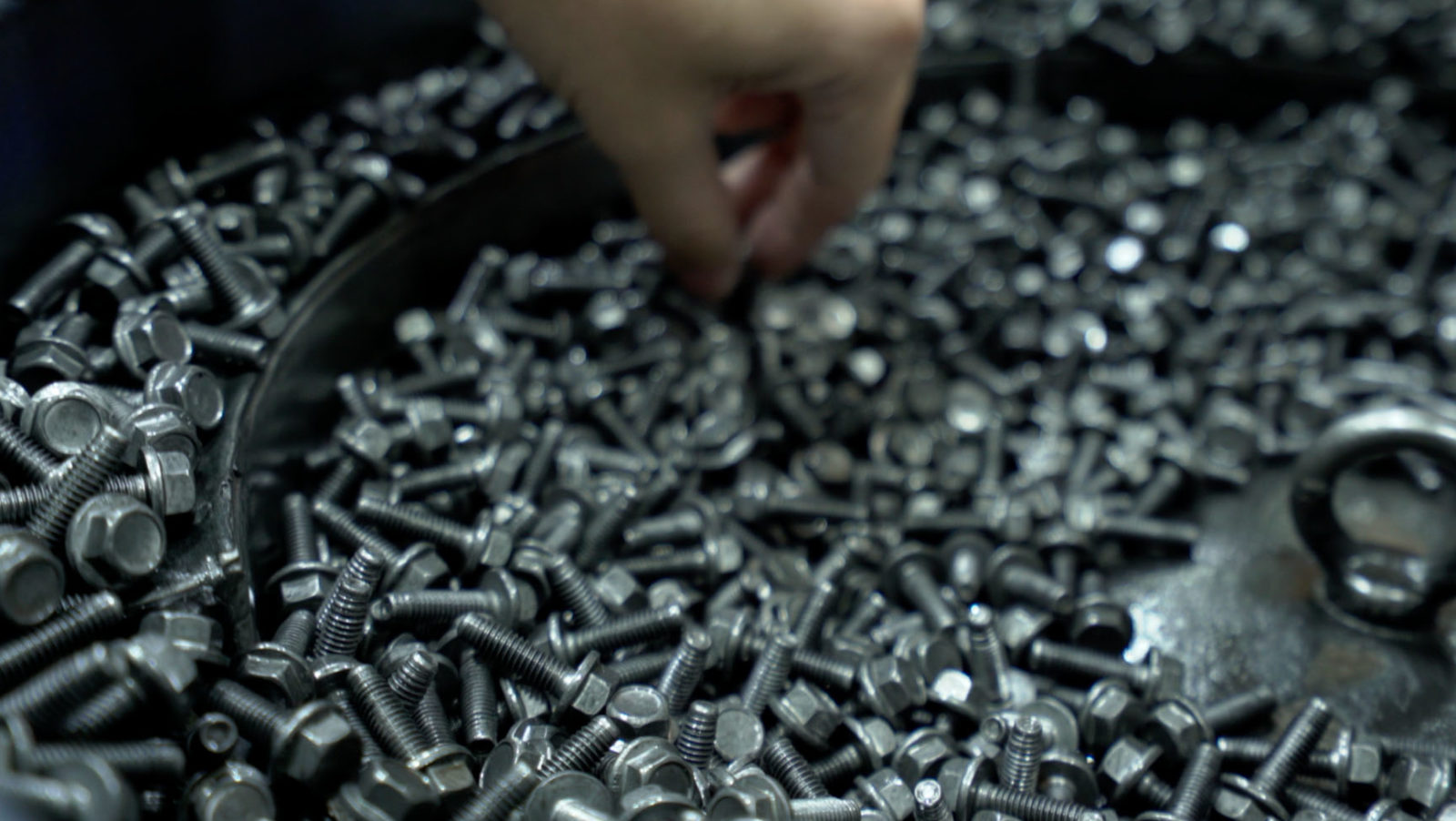
The nuts and bolts of AI: What’s next for Taiwan’s manufacturing sector?
Artificial intelligence (AI) is taking center stage in Taiwan’s manufacturing sector by driving change and boosting global competitiveness. Sumeeko Industries Company Limited – a metal fastener and screw manufacturer – expects to increase its production accuracy rates by 50%, and triple its efficiency by using AI.
For decades, a four-way partnership bringing together, government, academia, technology providers, and industry, has made Taiwan a powerhouse of manufacturing innovation and growth. Now, as competition from abroad rises and as its skilled workforce ages, Taiwan is betting that AI will help it stay ahead.
AI is certainly high on the policy and investment agenda. The government is to spend US$540 million in AI research over the next five years. And, Microsoft is creating a US$33 million AI hub in the capital, Taipei.
Meanwhile, in the southern city of Kaohsiung, the government’s Metals Industries Research and Development Center (MIRDC) is partnering with Microsoft to showcase and accelerate AI adoption on the nation’s factory floors.
Let’s take the example of one of Taiwan’s many highly successful metal fastener manufacturers, Sumeeko. Here, skilled engineers calibrate and maintain machines so that production lines run smoothly.
The company has already moved ahead with Internet of Things (IoT) technology that connects its machines to the cloud so that engineers can receive alerts when calibrations drift and error rates increase. While this is good start on the road to the future, it’s not enough.
By adopting AI, Sumeeko’s engineers will be able to understand how a machine is performing in real time, so it can be instantly readjusted and recalibrated. AI will also deliver predictive maintenance capabilities that can foresee problems before they appear so that machine parts can be replaced with close to zero downtime or breakdowns.
Sumeeko’s President, Alex Chen, regards AI as a big cost saver. “Our plant maintenance costs will reduce because AI’s predictive maintenance foresees problems before they become catastrophic and expensive to fix,” he says. “Costly screw molds can last longer because of reduced wear and tear from errors and inaccurate calibration.”
Chen also expects AI-driven processes will give his engineers new skills. “They will have a deeper understanding of how the production lines are running minute-by-minute. And, our customers can eventually enjoy higher quality products with minimum defects.”
“Thanks to AI, IoT, and big data analytics, we expect to see substantial improvements in time-saving on our production lines and a decrease in product wastage of more than 20 percent.”
Overall, Sumeeko is expected to triple its production efficiency and increase its fastener accuracy rate by 50 percent.
Chorng-Tyan Lin, Director of manufacturing R&D, MIRDC, adds, “Our next step is to learn about AI best practices from other industries and see what might work best for companies like Sumeeko, so they can be industry disrupters rather than followers.”
MIRDC’s Experience Center was set up to showcase new innovations and technology for the manufacturing industry. It’s a place where not only manufacturers but also students and professors can visit to learn and be inspired by the potentialities of new technologies like AI. More importantly, the center aids in training the talent of tomorrow to counter the dearth of young STEM employees.
“Our experience center is a good playground for students to learn real-world uses of AI,” Lin says. “We partner with schools to organize visits as well as recruit students to work on some of our projects in the field. Even before they graduate, they can have the experience of solving real industry problems and witness the possibilities of emerging technology.”
Lin adds that MIRDC are hoping for “a revolutionary change in the way we harness emerging technologies within the next two to three years. We believe we are one of the thought leaders who can enable this change.”
Read more about how Asia Pacific is transforming digitally:
- Hot properties – Beating the competition in sales with AI in Hong Kong
- Digital transformation to contribute more than US$1 trillion to Asia Pacific GDP by 2021; AI is primary catalyst for further growth
- How to win big in Asia’s Digital Transformation Game
- Apollo Hospitals – Bringing advanced healthcare to 300 million Indians, thanks to technology
- Real Digital Transformation: future-proof your business model
- Everyone must change their mindsets to win the never-ending digital skills game across Asia Pacific
- AI in the operating theater: Technology transforms cosmetic surgery in Korea